What is a Digital Twin?
A digital twin is a virtual reflection of a physical object, generally driven by marvels of:
- Internet of Things (IoT),
- Cloud, and
- Advanced Analytics.
A digital twin constantly collects real-time data and simulates it into the virtual replicate of the physical object. This virtual replicate then can be used to provide solutions to the problems experienced by the physical object.
The term ‘Digital Twin’ was coined by Michael Grieves in 2002. However, the concept of Digital Twin is as old as Apollo 13 (the 1970s). Though Apollo 13 was a failed moon mission, it hinted towards the inception of virtualization of the physical world. On its way, around 330,000 km from Earth; the Kennedy Space Centre received an SOS: “Houston, we have a problem”. The oxygen levels in the spacecraft had started declining fast. The dramatic rescue mission was started to bring the onboard astronauts back to the Earth. The key to this mission was that NASA had a physical replica of Apollo 13 on Earth. The Engineers performed a series of troubleshooting measures on the replica and came up with the best possible solution for bringing back the quickly declining Apollo 13. Rescuing all three members onboard was done successfully. This mission revolutionized the future of Space Exploration and it is also popularly known as a successful failure.
“Houston, we have a problem”.
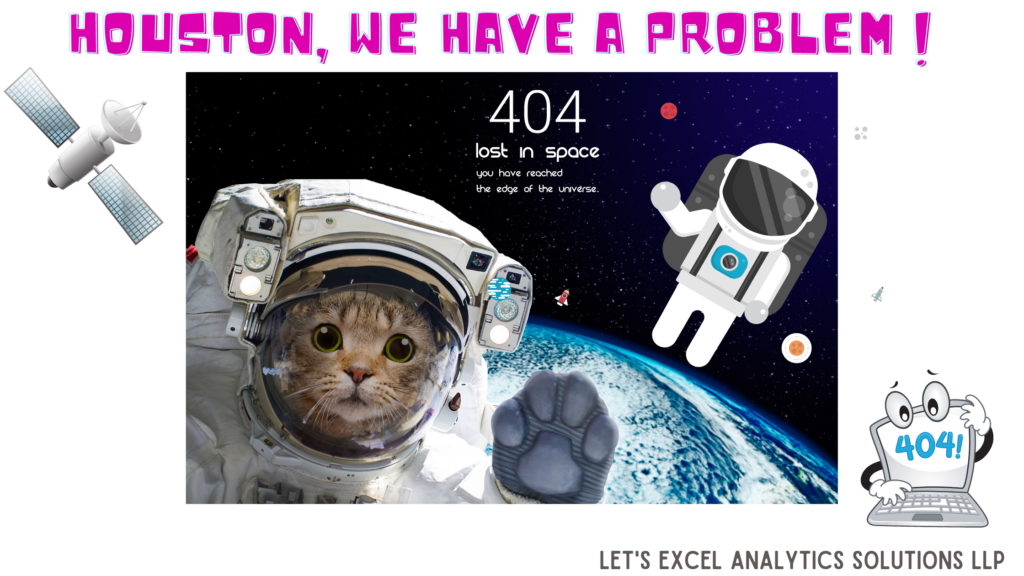
Unlike Apollo 13, all the replicas of current NASA programs are digitally and virtually monitored. NASA has been continuously using the real digital twin technology. It is used to solve the day-to-day problems encountered in the operation and maintenance of its space programs; without actually being physically present.
Another milestone in the history of digital twins was the launch of Predix by GE Digitals (a subsidiary of GE Electric). Predix is an Internet of Things (IoT) platform that secures cloud computing and data analytics. Used for improving the operational efficiencies of the machines. In 2015, Collin J Paris, Vice President of GE Global Research Center; demonstrated to the world:
- how a computer program could predictively diagnose malfunctions in the operation of a steam turbine and,
- even could perform the maintenance activities remotely.
GE has been continuously monitoring hundreds of such turbines using their digital twins for over a decade now.
Working of Digital Twin
- The physical object, also known as an asset, is designed to have many, sometimes hundreds, of sensors. These sensors capture real-time data (about almost everything) and send it across to its digital twin.
- The digital twin analyses this useful information. Further, mixes this information with the hundreds of other similar assets, using:
- the Internet of Things (IoT),
- cloud connectivity, and
- predictive data analytics.
- Additionally, the information shared with the digital twin is simulated to the various design features of the asset.
- The simulation is used to answer two important questions viz.,
- What could go wrong?
- What could be done about it?
- This knowledge is used to build a learning platform that makes digital twins smarter every time additional information is added.
Applications of Digital Twin
Use of digital twins in patient care
Philips is pioneering on the concept of what is referred to as the virtual representation of a patient’s health status, i.e., each patient would have a digital twin that enables the right type of treatment in the right way and at the right time. For example, if a patient presents with a particular symptom, its digital twin uses medical diagnosis data in combination with the patients’ medical history along with a variety of medical information available to build a digital model that recommends the patient-specific treatment modality with the best possible outcome. The digital twin also enables simulation of the treatment modality on the patient before implementing the procedure on the patient in the real case scenario. During the performance of the procedure, it ensures fidelity of the procedure and can even predict any unforeseen complication that can be averted in the first place. Moreover, all this information is stored in the cloud and can be retrieved anywhere at any time.
Use of digital twins in manufacturing
The digitalized twin of a manufacturing process uses IoT sensors that collect real-time process data continuously. The IoT sensors enable uninterrupted monitoring of the process. This increases the overall performance of the manufacturing process. Continuous monitoring also allows anticipation of the maintenance needs through the use of advanced analytics. This could reduce the possible process outages and downtimes that save millions of dollars. The amalgamation of advanced analytics and IoT can be used to manage the performance of the manufacturing process and which, in turn, improves the quality of the final product. It is important to note that the digital twin of a manufacturing process is not a single application but hundreds of interconnected applications. The communication between all these applications puts the process into a state of control.
The virtualization process is also taking over the most vital component of the manufacturing industry, i.e., supply chain management. The digital twin of the supply chain can automate the organizational processes. The twin can automate the purchasing and tracking of the assets and consumables based on the anticipated usage. If there is a shortage of raw material, the twin can assess the possible impacts on the operations and also offers the best-case scenario and solutions. This makes an organization prepared for overcoming the logistic challenges and hence improve the overall productivity of the organization
Future of Digital Twin Technology
The digital twin technology is rapidly expanding its applicability in almost every industry and, in fact, almost everywhere. Due to the adoption of the fourth industrial revolution, Industry 4.0, the market of the digital twin is expected to grow enormously. The global market of digital twins was valued at $3.1 billion in 2020 and is projected to grow $48.2 billion by 2026 at a Compound Annual Growth Rate (CAGR) of 58%.
The outbreak of COVID 19 has upheld the implementation of digital twins in business models, particularly in the biotechnology and pharmaceutical industries. The industry is gearing up to upgrade the existing infrastructure and adopt the digitalized technologies to avoid crippling losses due to frequent lockdowns. The Governments are also very keen on adopting the technology as can be seen in the design of smart cities across the world. The smart city initiative of Singapore is the best-fit example for the application of digital twin technology. This model combines different technologies to develop a digital version of the city’s resources, processes, and procedures. The digital version of the city enables superintend of the city using a simple computer program.
Conclusion
The new normal of the pandemic has redirected and reinforced the adoption of Digital twin technologies into every aspect of our lives. Digital twin technology is going to be a game-changer in the fields like continuous manufacturing. There are innumerable advantages of the adoption of the technology like cost leadership, environmental sustainability, economic stability, energy efficiency, etc. This is going to change the way our businesses have ever been managed. Let’s Excel Analytics Solutions LLP can support your organizational needs to develop digitalized tools for reinventing the business.
Curious to know more?